MANUFACTURING OF LDPE, HDPE AND PLASTIC GRANULES
LION RECYCLING UKRAINE
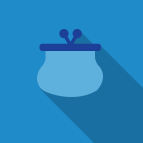
Replacing primary raw materials for secondary ones in the production cycle may lead to a total amount of savings as high as UAH 10 000 per tonne in your purchase.
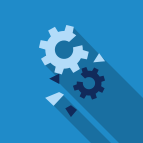
Using our secondary raw materials the life of the equipment is extended, in comparison with crude raw materials that contain inclusions.
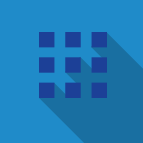
The quantity of defective products is so reduced by 15-20%: we do not buy raw materials from landfills, we use cleaning blocks, double-blowing system from dust and metal separation in crushing (2 blocks: for cleaning from ferrous and non-ferrous metals).

There is a required washing phase of granules / agglomerates with professional detergents during the manufacturing cycle.

While the manufacturing of the extrusion blow moulding granules, only a block of P72 grids (8 µm cells) is used; the replacement of grids is made at least in every 100 kg.

So as to get such materials that don’t contain impurities there is a dry cleaning unit in the crushing plant (dirt, dust, fine fraction, cardboard, moisture, polymer dust).

So as to eliminate any excessive fine-fraction grinding, our knives are regularly sharpened; as a result – 5-8 mm fractions (too big fractions clog the equipment, in consequence – downtime due to repairs).

The crushing plant is thoroughly cleaned during material transitions to prevent getting mixed (by type of polymers or colours).

We reduce the problems with logistics and warehouse accounting by using high-quality, standardized packing and packaging: clean, durable, well-knotted bags with a gross weight of 25.1 kg and with appropriate marking (material, date, shift).